Alexandra Lee
PAES Diagnosis Device

As part of an MIT undergraduate research opportunity, I designed a second iteration of a device to improve the diagnosis of Popliteal Artery Entrapment Syndrome (PAES), a condition that restricts blood flow in the leg. Current diagnostic methods are inconsistent and physically demanding for physicians. Our goal was to create a low-cost, open-source device that quantifies the force and angle required to provoke PAES symptoms during plantar flexion. This device would provide measurable, repeatable data while allowing physicians to focus on ultrasound imaging, ultimately improving diagnostic accuracy and supporting ongoing PAES research.

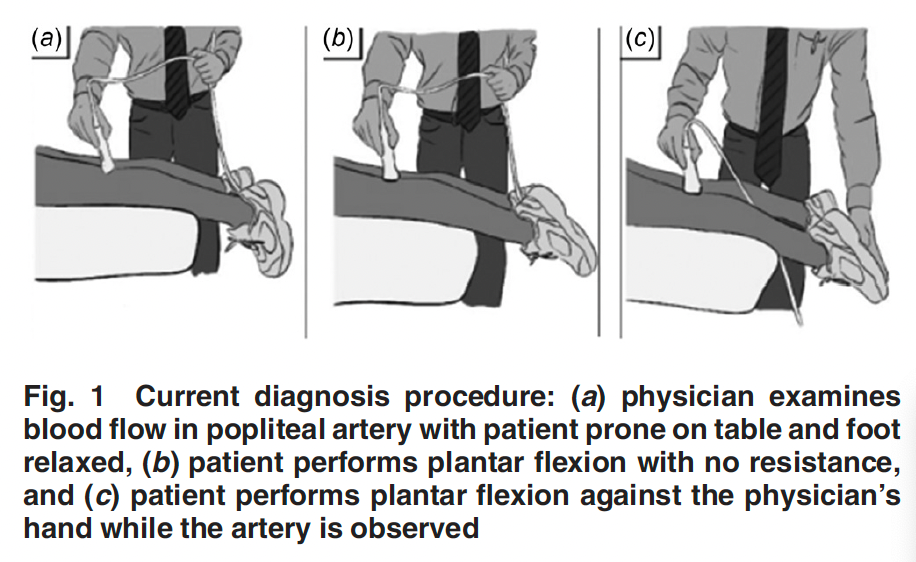

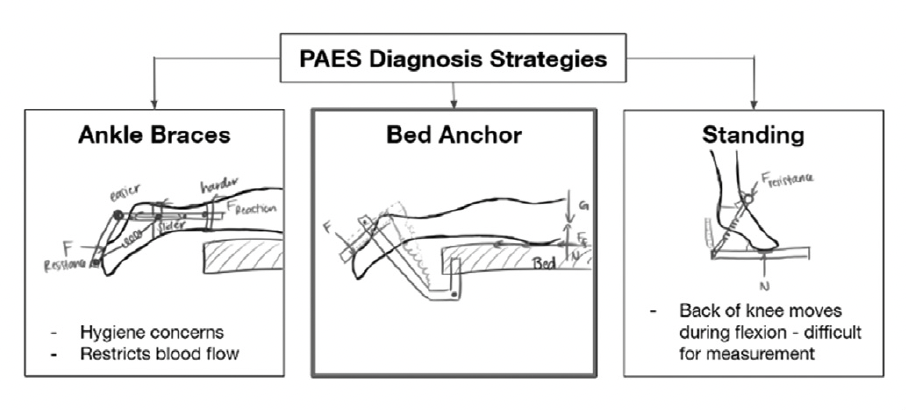

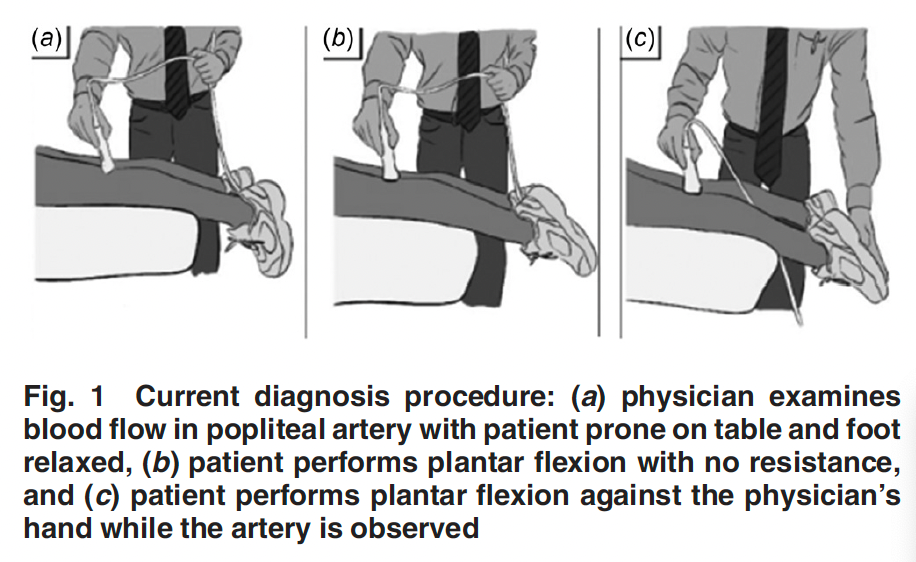

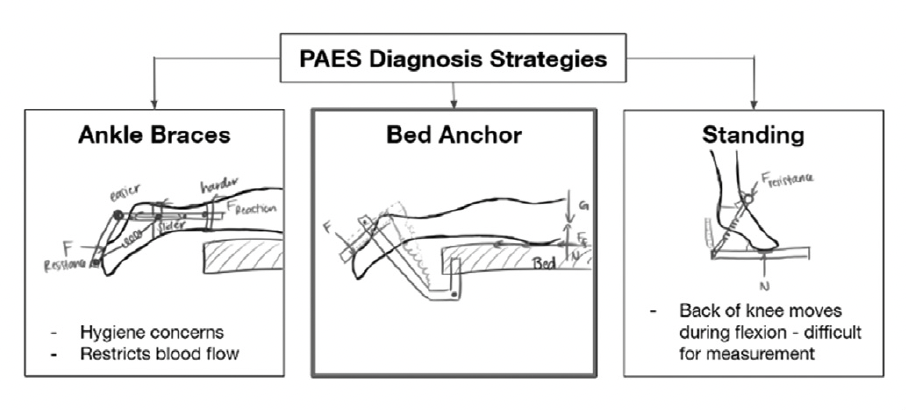
This project was a major learning experience in medical device design and the importance of user-centered engineering. I developed a strong understanding of how to balance functionality with the needs of both physicians and patients, improved my skills in component selection, and learned to manipulate the system for optimization and cost-effectiveness.
​
The project also helped me transition from a purely iterative approach to one grounded in predictive design, using calculations and analysis to guide early decisions. This was a significant shift in my engineering mindset, allowing me to think critically about the mechanical requirements of each component.
​
Finally, the collaborative nature of the design review process pushed me to embrace feedback and continuously refine my work. I not only improved the design itself but also my ability to think through complex problems. This experience reinforced the importance of precision, collaboration, and thoughtful design in creating real-world medical solutions.
Takeaways
-
CAD
-
Mechanics
-
Design analysis
-
Precision design
-
Problem solving
Process
Motivation
Popliteal Artery Entrapment Syndrome (PAES) is a condition that severely impacts blood flow to the leg, often leading to pain and cramping. Diagnosing PAES remains a challenge due to the lack of standardized, objective methods for provoking symptoms and measuring arterial occlusion. Current techniques, such as manual resistance during plantar flexion combined with ultrasound, are not only subjective but also physically taxing for physicians and difficult to replicate across different patients or diagnostic sessions.
​​​​​​​
​
Goals
The goal of the project was to create a low-cost, open-source device to improve the accuracy and ease of diagnosing PAES. By designing a system that applies adjustable resistance and quantifies the force and angle at which arterial occlusion occurs, we aimed to provide doctors with reliable, measurable data. This device also helps reduce the physical burden on physicians by allowing them to focus on ultrasound imaging, rather than manually applying resistance.
Based on conversations with an orthopedic surgeon and PAES specialist, we created the following design requirements. The device needed to:
-
Provide adjustable resistance during plantar flexion to provoke PAES symptoms at various force levels
-
Measure and log both the resistance force and the angle of foot flexion, allowing for objective data collection to compare between patients and over time
-
Leave the back of the knee open for ultrasound diagnosis without obstructing blood flow
-
Minimize physical input from the physician, allowing them to focus on performing ultrasound imaging.
-
Accommodate a wide range of foot sizes while maintaining comfort for patients during the diagnostic process
-
Be cost-effective and open-source, so the device could be easily replicated and contribute to PAES research
​
These design requirements were essential to create our device to improve the diagnostic process for PAES while advancing research in the field.
Progress
​
Understanding User Needs
The first part of the project involved understanding the limitations of current PAES diagnostic methods and the first iteration prototype of the diagnosis device. After discussions with Dr. Dowlatshahi, an orthopedic surgeon specializing in PAES, we identified the key challenges: the difficulty in manually applying consistent resistance during diagnosis, the need to measure the force and angle at which occlusion occurs, the strain on physicians who must simultaneously resist the patient’s plantar flexion and perform ultrasound imaging, and the lack of consistency in a hydraulic approach from the first iteration prototype. This informed our design goals and functional requirements, ensuring the device would provide a more reliable solution.
Brainstorming and Initial Design
​The design process began with brainstorming ideas on how best to provide adjustable resistance during plantar flexion. We explored improving the hydraulic system, using springs, or creating a leadscrew and motor system to apply resistance while measuring force. The first iteration relied on hydraulics, but due to issues with consistency and leaks, we shifted to a more reliable leadscrew and motor system. This system allowed for controlled, repeatable resistance while providing the required force measurement.
​​
The design also needed a footplate attached to the leadscrew, which the patient could push against during plantar flexion, and a linear support system to allow the leadscrew to function smoothly. I had to consider details like attaching the device to a hospital bed for stability and ensuring the footplate could accommodate different foot sizes comfortably. All components were sourced from off-the-shelf parts, so I needed to match the design requirements for force and stiffness based on the loads.
​
Iterative Design and Reviews
The design phase included a CAD model and part selection based on catalog specifications. During my first design review, I was heavily critiqued because my system was oversized and inefficient. My mentor pointed out that the leadscrew, linear supports, and other components could be downsized to reduce cost and improve performance without compromising stability. I was introduced to failure analysis and how to apply fundamental equations to real-world design. Even when there wasn't a Google-able equation for the analysis, I learned to create one and really problem-solve. This was a key learning experience in optimizing a design beyond just meeting the requirements – calculating stiffness, material strength, and geometries became crucial as I revised the design.
​
Final Prototype
The final design featured a motor-driven leadscrew system that applied adjustable resistance during plantar flexion while measuring both the force applied and the angle of flexion. The footplate was mounted on linear supports, the back of the knee remained open for ultrasound imaging, and the system was mounted to the hospital bed. All measurements were recorded in real-time and displayed on a graphical user interface (GUI), allowing the physician to focus on the ultrasound while logging valuable diagnostic data. This data can be used to contribute to ongoing PAES research.
​
Challenges and Next Steps
Throughout the process, one of the biggest challenges was learning to balance theoretical design with practical constraints. While I initially relied heavily on catalog specifications, I learned to use engineering calculations on a design spreadsheet to refine my choices, making the system both more cost-effective and better suited to the real-world application.
​
The next steps for this project involve further testing of the prototype, particularly focusing on the electronics for force measurement. There is also potential to integrate additional features, such as automated data analysis and enhanced adjustability, to further ease the physician's workload.
​
​
​